PROFESJONALNY KOLEKTOR CHŁODZONY CIECZĄ (5)
z dnia: 2013-10-17
Marynizacja silników stosowanych w różnego rodzaju maszynach i pojazdach lądowych nie jest trudna, ale jak się naprawdę wie co jest ważne.
Już w poprzednich odcinkach Tadeusz Lis wyjaśnił dlaczego kolektor wydechowy chłodzony cieczą jest tak ważnym elementem tej adaptacji.
Pod poprzednimi newsami poświęconymi temu zagadnieniu Tadeusz odpowiadał też na różne pytania.
Kto nie czytał - warto powrócić do zaległej lektury.
Między innymi przeczytacie tam dlaczego niektóre silniki samochodowe do tego się nie nadają.
Żyjcie wiecznie !
Don Jorge
------------------------------
Wykonujemy profesjonalny kolektor chłodzony cieczą
W tym foto-komiksie pokażę jak krok po kroku wykonać profesjonalny kolektor chłodzony cieczą. Konstrukcja w sensie ideowym jest analogiczna jak w poprzednio opisanym, prymitywnym kolektorze – natomiast do jego wykonania wykorzystamy możliwości, jakie daje dobrze wyposażony warsztat mechaniczny. Pokazujemy Wam klasyczne wykonanie elementów, z wykorzystaniem typowych maszyn. Jeżeli jednak w zasięgu Waszych możliwości nie ma takiego warsztatu, to bardzo atrakcyjną kosztowo alternatywą jest wycięcie elementów na wycinarce laserowej lub wodnej oraz ograniczenie prac do odpowiedniego wygięcia blach, pocięcia rurek oraz pospawania. Jednak wbrew pozorom, dla amatora może być to trudniejsze, gdyż wymaga wykonania bardzo precyzyjnego rysunku w programie typu AutoCAD. Przestrzegam Was, że bez zbudowania modelu z kartonu w skali 1:1 nie jest wcale trudno stwierdzić po niewczasie, że zabrakło nam 5 mm do zamontowania alternatora lub kolektor mieści się nad rozrusznikiem – ale klucz do przykręcenia przewodów zasilających rozrusznik musiałby być wykonany z plasteliny o żywym i błyskotliwym umyśle. Raczej rzadkie. Tym niemniej, jeżeli ktoś z Kolegów podejmie ten trud – to łamy SSI są zawsze otwarte i dobry komplet rysunków wykonawczych byłby bezcenny. Nawet jeżeli będzie dotyczył tylko jednego typu silnika. Ale weźmy się do przyjemnej, relatywnie prostej pracy. Punktem wyjścia będzie pozyskanie kawałka blachy ze stali 316L grubości 8 mm i o wielkości, która wynika z rozstawu okien wydechowych w głowicy (Foto.1). Na blasze trasujemy wymiary zewnętrzne i po jej solidnym umocowaniu wycinamy ściernicą prostokątny kształt głównej ścianki nośnej – dotykającej przez uszczelkę do głowicy silnika (Foto.2). Jeżeli nie wierzycie, że będziecie w stanie równo wyciąć krawędzie wytnijcie obrys frezem piłkowym. W każdym wypadku skontrolujcie poprawność cięcia w sposób pokazany na fotografii (Foto.3). Jeżeli przy cięciu ściernicą odchyłki wyniosą kilka dziesiątych milimetra – nie ma dramatu. Wygubimy to przy spawaniu. Ale więcej –nie.
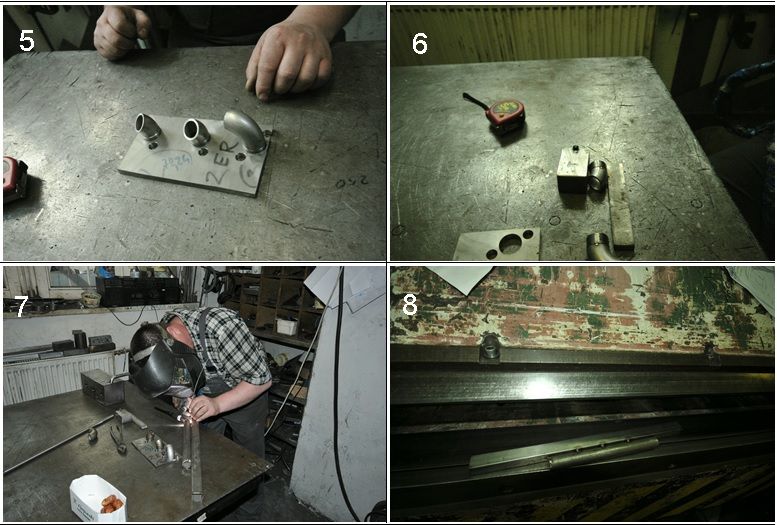 Teraz jest czas na wykonanie otworów pilotowych, które metodą kolejnych powierceń osiągną właściwą średnicę. Na fotografii podpowiedź z dobrej praktyki warsztatowej. W twardej blasze otwory pilotowe dobrze jest wykonywać nie cienkim, mało sztywnym wiertłem, ale znacznie sztywniejszym nakiełczakiem (Foto.4). Wiem, że dla doświadczonych Kolegów takie rady mogą wydawać się trywialne, ale po listach które dostajemy z Jurkiem wiemy, że wielu Czytelników dopiero zaczyna swoją przygodę z budową lub przebudową jachtów i staje przed pytaniami, przed którymi stanęło już dziesiątki żeglarzy wcześniej. Oczywiście do wykonania otworów nie musimy używać frezarki, wystarczy zwykła wiertarka stołowa, którą macie w garażu. Jednak nie próbujcie wykonywać ich ręczną wiertarką, gdyż będzie potem kłopot z precyzyjnym montażem rurek, przez które przechodzą śruby mocujące kolektor do bloku. Teraz wykonamy krytycznie ważne rurki wyprowadzające spaliny do komory rozprężnej. Sugeruje, abyście wykonali je dokładnie tak, jak pokazaliśmy to na fotografii – łącząc krótką tuleję (8 mm – tyle co grubość blachy) z kolanem hamburskim (Foto.5 i 6). Wprawdzie przy pewnym zapale można by osadzić kolano bezpośrednio w skośnym otworze, ale jego wykonanie byłoby trudne. Również nie spawajcie kolan bezpośrednio do płyty – będzie Wam je trudno ustawić, o czym za chwilę.
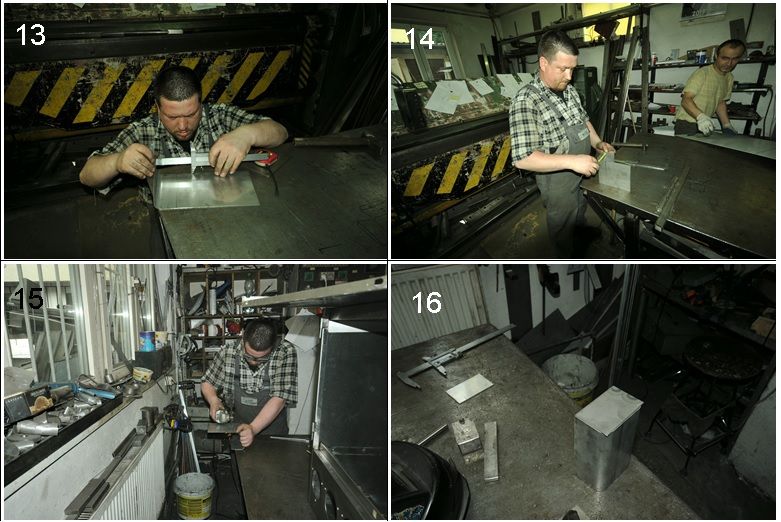 Osadzacie teraz króćce w płycie i obracając je w otworach znajdujecie ich optymalne położenie. Główna idea profesjonalnie wykonanego kolektora polega na tym, że dzięki tym dyszom i zaokrąglonym krawędziom komory rozprężnej uzyskacie bardzo pożądany ruch wirowy spalin. Dzięki temu woda chłodząca będzie odbierać od nich intensywnie ciepło. Tak wykonany kolektor daje Wam bardzo przyjemny, basowy gang silnika i płaszcz zewnętrzny na tyle chłodny, że spokojnie będziecie mogli położyć na nim rękę. Bezcenne z punktu widzenia bezpieczeństwa pożarowego – patrz wcześniejszy opis pożaru na Holly wskutek radosnej twórczości pana Andrzeja Ch.
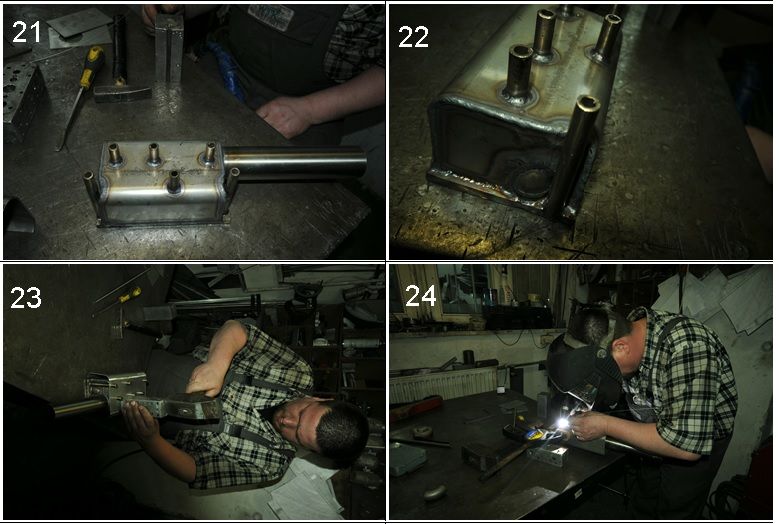 Teraz wykonamy przeginak (wzornik), który posłuży nam do wykonania zaokrągleń w blasze, z której ukształtujemy komorę rozprężną (Foto.7). Na fotografii prosty trick warsztatowy, a na następnej – jak wykorzystać wzornik na giętarce (Foto.8). Wyznaczając linię gięcia (możecie to również zrobić na małej prasce w garażu, zaimprowizowanej z samochodowego podnośnika hydraulicznego) musicie starannie odmierzyć jej odległość od krawędzi, która będzie spawana do naszej powierconej płyty. Wykonujemy gięcie (Foto.9.10) i na następnej fotografii widzicie estetycznie ukształtowaną krawędź komory rozprężnej (Foto.11). Upewniamy się, że odległość jest taka, jaką zaprojektowaliśmy (Foto.12). Zazwyczaj wszystko jest w porządku, zatem możecie wyznaczyć następną, pożądaną linię gięcia (Foto.13). Powtarzamy operację, kontrolujemy odległość (Foto.14) oraz ucinamy zbędny naddatek (Foto.15). Był on nam potrzebny, abyśmy mogli wygodnie operować na giętarce. Jak widzimy na następnej fotografii mamy już gotową ściankę wewnętrznej komory – idealnie dopasowaną do płyty. Teraz z uciętego kawałka dopasowujemy dekiel (Foto.16). Może trochę wystawać – oszlifujecie go potem. Następną operacją jest wywiercenie otworów pod tulejki (Foto.17). Jest to bardzo proste, bo jako wzorcowej płyty wiertarskiej użyjecie przygotowanej uprzednio blachy. Tulejki tniecie z naddatkiem, niezbędnym, aby wyprowadzić je nad powierzchnię zewnętrznego płaszcza (Foto.18). Osadzacie je na lekki wcisk w przygotowanej płycie (Foto.19). Dzięki temu nie będzie kłopotu z ich prostopadłością i całość da się łatwo złożyć, gdy będziecie pracowali bez pomocnika.
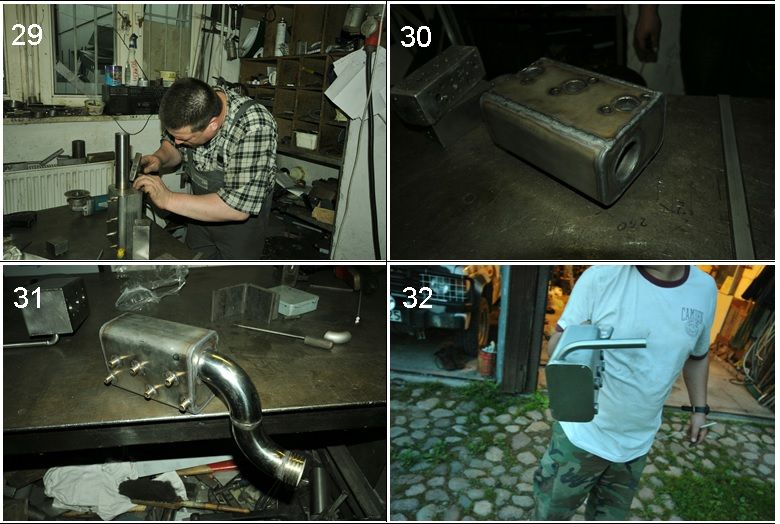 Nic już nie stoi na przeszkodzie, aby zamknąć pracę nad komorą rozprężną (Foto.20.21.22). Teraz w analogiczny sposób doginamy płaszcz zewnętrzny (Foto.23) używając aluminiowego pobijaka – chodzi o to, aby nie uszkodzić powierzchni blachy (będziecie ją polerować). W tym wypadku użycie typowego, gumowego młotka blacharskiego nie zdałoby egzaminu – blacha jest zbyt twarda. Na następnej fotografii pokazano jak sprawdzić prostopadłość ścianek płaszcza (Foto.25). Zwykle będą potrzebne przed spawaniem drobne poprawki. Teraz uwaga – ważna operacja (Foto.26). Musicie sfazować krawędź płyty mocującej, tak, aby zagięty płaszcz zlicował się z płaszczyzną płyty. Wykonujecie to tarczą szlifierską – rezultat, na następnej fotografii (Foto.27). Jak widać, dzięki temu doświadczony spawacz uzyskał idealnie prostopadłe ścianki zewnętrzne (Foto.28).
W następnym ruchu dopasowujemy dekiel przedni, wpuszczając go do wnętrza płaszcza (Foto.29). Pozwoli to na uzyskanie estetycznej, zaokrąglonej krawędzi spawu w następnym ruchu (Foto.30). Dospawujemy kształtową rurę wydechową, pamiętając, aby końcówka miała nacięcia do węża wydechowego. Zwróćcie uwagę, czym się różni wprowadzenie wody, od amatorskiej i bardzo niebezpiecznej konstrukcji Andrzeja Ch., którą opisałem w poprzednich artykułach (Foto.33). Na koniec ważny szczegół konstrukcyjny. Warto jest naspawać wytoczone, grube podkładki, które przeniosą obciążenia łbów śrub mocujących kolektor do głowicy (Foto.34). Bez nich dociągając śruby moglibyście pogiąć blachę, a nawet rozszczelnić spawy.
Ostatnia fotografia pokazuje, jak montujecie kolektor na silniku (Foto.35). Ze względów estetycznych użyjcie polerowanych na lustro śrub kołpakowych. Będą cieszyły oko Waszych kobiet – a to ważne. Widoczna na fotografii (Foto.33) za długa rurka doprowadzająca wodę do płaszcza zostanie przycięta już na jachcie – gdy będzie wiadomo, jak podłączyć węże wody chłodzącej. Kolektor jest gotowy – w następnym odcinku wyposażymy nasze maleństwo w wymiennik ciepła oraz pompę wody zaburtowej. A potem – już tylko próby w ogródku na zaimprowizowanym stanowisku testowym przed finalnym montażem (Foto. 36).
Tadeusz.
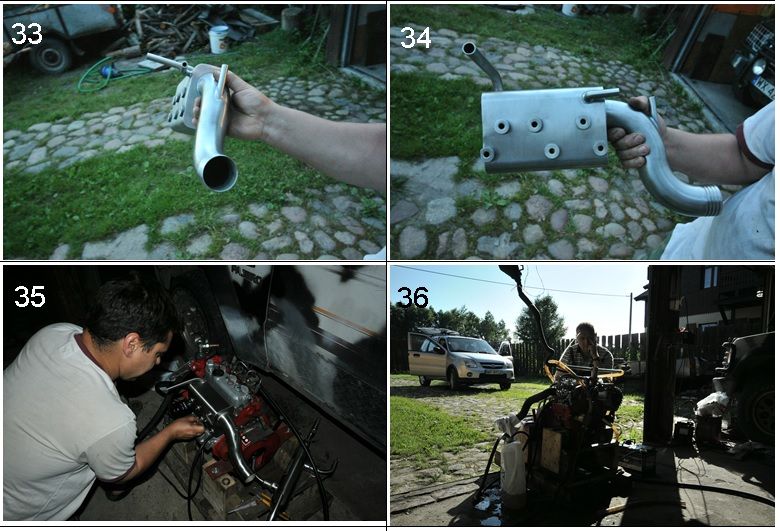 Autor dziękuję firmie pana Józefa Bujalskiego za pomoc w zorganizowaniu sesji fotograficznej na potrzeby Czytelników Subiektywnego Serwisu Informacyjnego Jerzego Kulińskiego. W tym warsztacie wykonuje większość trudnych prac związanych z obróbką skrawaniem metali i nigdy się nie zawiodłem. Koszty jednostkowe godziny są wysokie (jak jakość), ale finalne ceny usług niskie – co jest charakterystyczne dla zawodowców, którzy w pierwszym podejściu są w stanie wykonać dowolnie skomplikowany prototyp, bez konieczności wykonywania poprawek ( http://panoramafirm.pl/mazowieckie,,warszawa,wawer,strusia,91/slusarstwo_jozef_bujalski-tdcsy_pyp.html#tab )
|