MONTAŻ SILNIKA
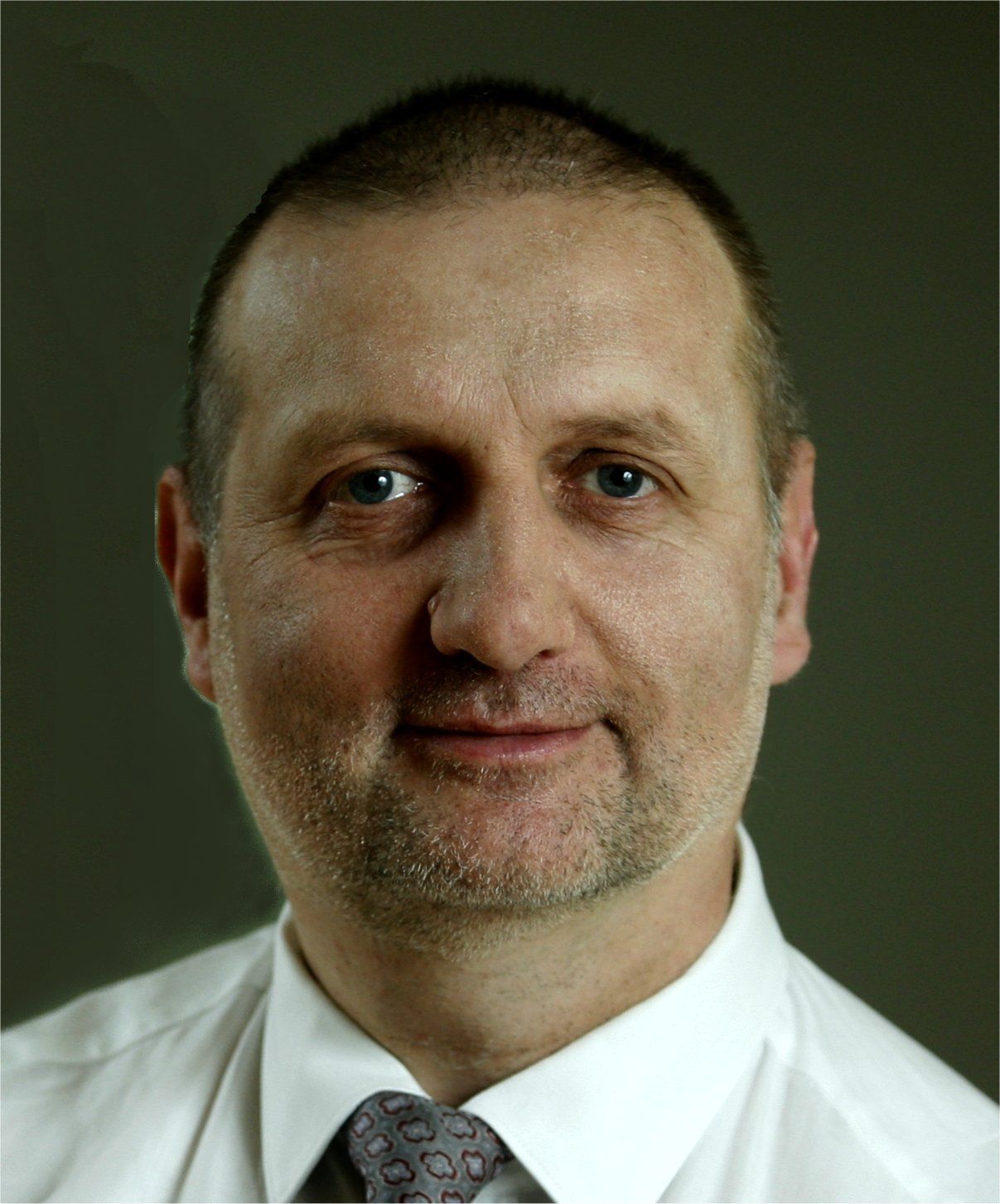
Po pierwsze - ustawienie jachtu, tak aby spoczywał na łożu (kobyłkach) dokładnie poziomo i bez żadnego przechyłu wcale nie jest takie proste. Bo mowa jest o jachcie balastowym, a nie o łódeczce.
Po drugie - nawet jachty produkowane wielkoseryjnie w stoczniach zdarza się, że nie są idealnie symetryczne, zwłaszcza w cześci rufowej. A więc i fundament silnika też nie będzie idealnie symetryczny.
Przećwiczyłem to.
Żyjcie wiecznie !
Don Jorge
----------------------------
Właściwa pochwa wymaga właściwego łoża
W niniejszym artykule opiszemy, jak wykonać łoże do silnika – w wariancie dla jachtu laminatowego oraz drewnianego. Geometria jest zdeterminowana przebiegiem pochwy w kadłubie. Jak doprowadzić do szczęśliwego skojarzenia z dużą dokładnością – w następnym artykule.
Ale dzisiaj - łoża. Na jachtach drewnianych nie jest to wielki problem – po prostu wykonujemy dwa solidne wzdłużniki denne (legary) i mocujemy je do wręg rys. 1. Proszę zwrócić uwagę w jaki sposób mocowana jest belka poprzeczna do wręg oraz legary do belek poprzecznych.
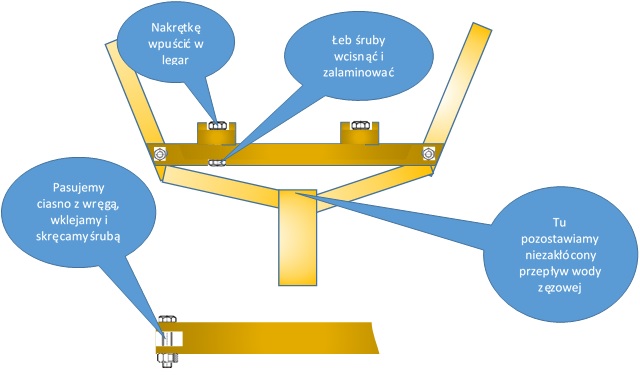
W niniejszym artykule opiszemy, jak wykonać łoże do silnika – w wariancie dla jachtu laminatowego oraz drewnianego. Geometria jest zdeterminowana przebiegiem pochwy w kadłubie. Jak doprowadzić do szczęśliwego skojarzenia z dużą dokładnością – w następnym artykule.
Ale dzisiaj - łoża. Na jachtach drewnianych nie jest to wielki problem – po prostu wykonujemy dwa solidne wzdłużniki denne (legary) i mocujemy je do wręg rys. 1. Proszę zwrócić uwagę w jaki sposób mocowana jest belka poprzeczna do wręg oraz legary do belek poprzecznych.
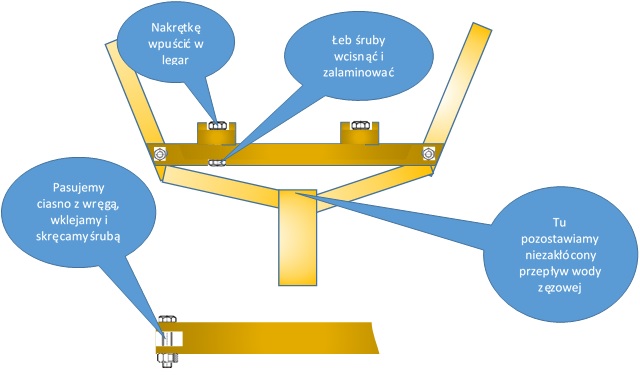
Rysunek 1.
.
Najlepszym materiałem na konstrukcję fundamentu jest wysezonowana dębina lub iroko. Jednak w przypadku iroko sugerowałbym sklejenie legarów z dwóch części – na przemiennie lewa i prawa strona, ponieważ niektóre gatunki iroko potrafią pękać pod obciążeniem. Poznajemy je po tzw. delikatnej kobyłce – czyli wygięciu się w mały łuk po jednej stronie w procesie schnięcia
Po wykonaniu legarów i ich wstępnym zmontowaniu (jeszcze ich nie kleimy na wypadek gdyby zaszła konieczność korekty ich geometrii) przygotowujemy ze sklejki model silnika pokazany na rysunku nr 3
Najlepszym materiałem na konstrukcję fundamentu jest wysezonowana dębina lub iroko. Jednak w przypadku iroko sugerowałbym sklejenie legarów z dwóch części – na przemiennie lewa i prawa strona, ponieważ niektóre gatunki iroko potrafią pękać pod obciążeniem. Poznajemy je po tzw. delikatnej kobyłce – czyli wygięciu się w mały łuk po jednej stronie w procesie schnięcia
Po wykonaniu legarów i ich wstępnym zmontowaniu (jeszcze ich nie kleimy na wypadek gdyby zaszła konieczność korekty ich geometrii) przygotowujemy ze sklejki model silnika pokazany na rysunku nr 3

Rysunek 2.
.
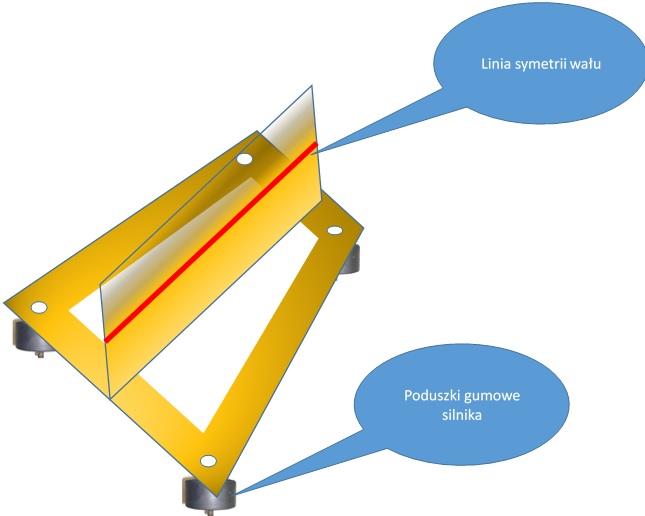
Rysunek 3.
.
Posłuży nam to precyzyjnego wyznaczania osi wału i zaoszczędzi mnóstwa kłopotów. Po starannym zmontowaniu łoża po prostu włożycie silnik na wystające 4 szpilki poduszek – i już. Można to spokojnie zrobić w pojedynkę.
Pionową sklejkę mocujemy pod kątem prostym i na podstawie pomiarów wysokości osi silnika wykreślamy oś jego wału. Oczywiście pamiętamy, że w czasie pomiarów silnik powinien już stać na poduszkach przykręconych do łap (na zewnątrz jachtu). Dotyczy to zwłaszcza tzw. poduszek progresywnych.
Dodatkowo do krawędzi modelu przykręcamy kątomierz szkolny wraz z pionem linkowym, który posłuży nam do weryfikacji poprawności wyznaczenia kąt pochylenia silnika (rys. 4)
Posłuży nam to precyzyjnego wyznaczania osi wału i zaoszczędzi mnóstwa kłopotów. Po starannym zmontowaniu łoża po prostu włożycie silnik na wystające 4 szpilki poduszek – i już. Można to spokojnie zrobić w pojedynkę.
Pionową sklejkę mocujemy pod kątem prostym i na podstawie pomiarów wysokości osi silnika wykreślamy oś jego wału. Oczywiście pamiętamy, że w czasie pomiarów silnik powinien już stać na poduszkach przykręconych do łap (na zewnątrz jachtu). Dotyczy to zwłaszcza tzw. poduszek progresywnych.
Dodatkowo do krawędzi modelu przykręcamy kątomierz szkolny wraz z pionem linkowym, który posłuży nam do weryfikacji poprawności wyznaczenia kąt pochylenia silnika (rys. 4)
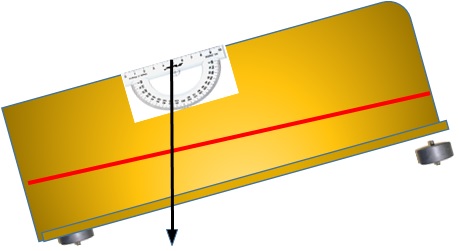
Rysunek 4.
.
Interesuje Was zapewne jak przymocować poduszki do drewnianego łoża, skoro większość z nich ma standardowo od dołu szpilki.
Odpowiedź brzmi: nie mocować. Od lat stosuje sprawdzone rozwiązanie, które polega na położeniu na legary stalowego ceownika, w którym będą gwintowane otwory do szpilek (foto 5 ). Płaskownik ma wyfrezowane lub wyszlifowane łezki, które umożliwiają jego regulację w przód i w tył.
W warunkach polowych wykonujemy je poprzez szereg sąsiadujących nawierceń i wyrównanie miniaturową ściernicą lub pilnikiem (najlepiej z nasypem diamentowym).
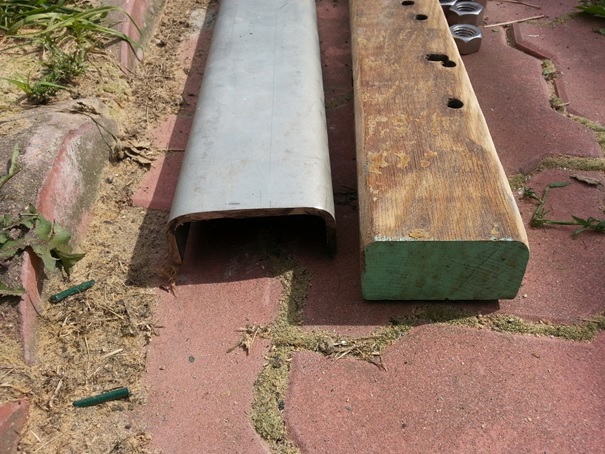
Rysunek 5 - stalowa nakładka na drewniane łoże pod silnik
Interesuje Was zapewne jak przymocować poduszki do drewnianego łoża, skoro większość z nich ma standardowo od dołu szpilki.
Odpowiedź brzmi: nie mocować. Od lat stosuje sprawdzone rozwiązanie, które polega na położeniu na legary stalowego ceownika, w którym będą gwintowane otwory do szpilek (foto 5 ). Płaskownik ma wyfrezowane lub wyszlifowane łezki, które umożliwiają jego regulację w przód i w tył.
W warunkach polowych wykonujemy je poprzez szereg sąsiadujących nawierceń i wyrównanie miniaturową ściernicą lub pilnikiem (najlepiej z nasypem diamentowym).
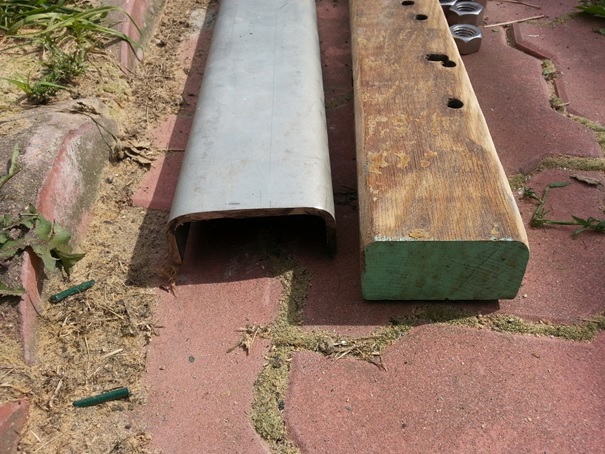
Rysunek 5 - stalowa nakładka na drewniane łoże pod silnik
.
Zastosowanie ceownika pozwala na bardzo wygodne wysunięcie silnika do wnętrza kabiny w pojedynkę. Ponieważ tak jak pokazałem to na rysunku w łożu są wystające na niewielką wysokość szpilki, to wystarczy nieco podważyć ceownik z obu strony i po rozpięciu sprzęgła płynnym ruchem przesunąć cały silnik do przodu łodzi. W Donaldzie jest przygotowany do tego dolny, rozbieralny schodek zejściówki. W ten sposób mam wygodny dostęp do pompy paliwowej, alternatora i rozrusznika. Bez problemu można wyregulować precyzyjnie luzy zaworowe, wymienić świece żarowe lub wtryskiwacze.
Zanim opiszę, jak wykonuje łoże laminatowe, pozwolę sobie na krótką dygresję. Wieloletnie doświadczenie warsztatowe nauczyło mnie, że w przypadku elementów gabarytowych (silnik, przekładnia, zbiorniki paliwa, wody, fekaliów, itp. - zwłaszcza tych o większych wymiarach lub ciężarach) ich mocowanie we wnętrzu jachtu POWINNO BYĆ WYŁĄCZNIE WYKONYWANE ZA POMOCĄ MOCOWANYCH NA STAŁE SZPILEK, WYKONANYCH Z GWINTOWANEGO PRĘTA WYSOKIEJ JAKOŚCI (316l). Pozwoli to ich na łatwy demontaż, a tym samym staranną konserwację trudno dostępnych przestrzeni (co kilka lat) ukrytych pod nimi. Wysoka jakość szpilek oznacza tutaj, że jeżeli macie możliwość zakupu pręta, gdzie gwint jest walcowany i nagniatany, a nie nacinany maszynowo - to zróbcie to. O zaletach takich gwintów dla hobbystów, tutaj: http://yadda.icm.edu.pl/yadda/element/bwmeta1.element.baztech-article-BAR0-0057-0015/c/httpwww_bg_utp_edu_plartpe42010probeksp42010163175.pdf
Dlaczego inne rozwiązania uważam za ewidentnie błędne technologicznie? Ponieważ na małym jachcie nawet jeżeli macie przyjaciela, który Wam w czasie montażu służy drugą parą rąk, to i tak nie ma tam dla niego miejsca. Przy osadzaniu szpilek trzeba bezwzględnie pamiętać o:
a. zostawieniu co najmniej jednej średnicy gwintu poniżej dna szpilki (zaraz to wyjaśnię)
b. starannym odłuszczenie gwintu przed wklejeniem – najlepiej spranym kawałkiem flaneli nasączonej acetonem. Szpilka jest dobrze oczyszczona, jeżeli po paru obrotach na zaciśniętej tkaninie udającej nakrętkę zostaje wygnieciony ślad bez najmniejszej smugi smaru.
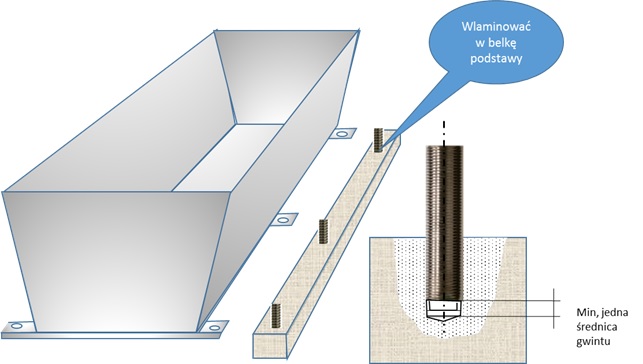
Rysunek 6 - osadzenie szpilek w laminatowym elemencie konstrukcyjnym. Dla uproszczenia na widoku pominąłem górną część przykładowego zbiornika ze stali na wodę lub paliwo.
Zastosowanie ceownika pozwala na bardzo wygodne wysunięcie silnika do wnętrza kabiny w pojedynkę. Ponieważ tak jak pokazałem to na rysunku w łożu są wystające na niewielką wysokość szpilki, to wystarczy nieco podważyć ceownik z obu strony i po rozpięciu sprzęgła płynnym ruchem przesunąć cały silnik do przodu łodzi. W Donaldzie jest przygotowany do tego dolny, rozbieralny schodek zejściówki. W ten sposób mam wygodny dostęp do pompy paliwowej, alternatora i rozrusznika. Bez problemu można wyregulować precyzyjnie luzy zaworowe, wymienić świece żarowe lub wtryskiwacze.
Zanim opiszę, jak wykonuje łoże laminatowe, pozwolę sobie na krótką dygresję. Wieloletnie doświadczenie warsztatowe nauczyło mnie, że w przypadku elementów gabarytowych (silnik, przekładnia, zbiorniki paliwa, wody, fekaliów, itp. - zwłaszcza tych o większych wymiarach lub ciężarach) ich mocowanie we wnętrzu jachtu POWINNO BYĆ WYŁĄCZNIE WYKONYWANE ZA POMOCĄ MOCOWANYCH NA STAŁE SZPILEK, WYKONANYCH Z GWINTOWANEGO PRĘTA WYSOKIEJ JAKOŚCI (316l). Pozwoli to ich na łatwy demontaż, a tym samym staranną konserwację trudno dostępnych przestrzeni (co kilka lat) ukrytych pod nimi. Wysoka jakość szpilek oznacza tutaj, że jeżeli macie możliwość zakupu pręta, gdzie gwint jest walcowany i nagniatany, a nie nacinany maszynowo - to zróbcie to. O zaletach takich gwintów dla hobbystów, tutaj: http://yadda.icm.edu.pl/yadda/element/bwmeta1.element.baztech-article-BAR0-0057-0015/c/httpwww_bg_utp_edu_plartpe42010probeksp42010163175.pdf
Dlaczego inne rozwiązania uważam za ewidentnie błędne technologicznie? Ponieważ na małym jachcie nawet jeżeli macie przyjaciela, który Wam w czasie montażu służy drugą parą rąk, to i tak nie ma tam dla niego miejsca. Przy osadzaniu szpilek trzeba bezwzględnie pamiętać o:
a. zostawieniu co najmniej jednej średnicy gwintu poniżej dna szpilki (zaraz to wyjaśnię)
b. starannym odłuszczenie gwintu przed wklejeniem – najlepiej spranym kawałkiem flaneli nasączonej acetonem. Szpilka jest dobrze oczyszczona, jeżeli po paru obrotach na zaciśniętej tkaninie udającej nakrętkę zostaje wygnieciony ślad bez najmniejszej smugi smaru.
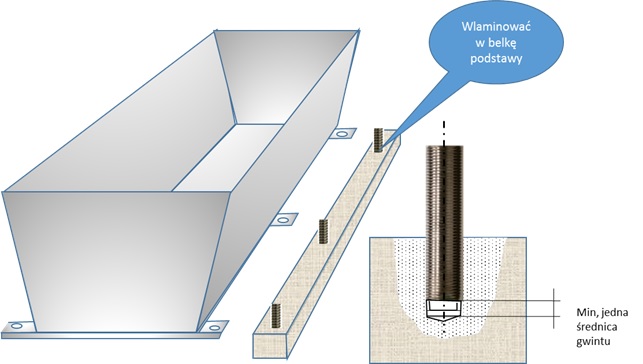
Rysunek 6 - osadzenie szpilek w laminatowym elemencie konstrukcyjnym. Dla uproszczenia na widoku pominąłem górną część przykładowego zbiornika ze stali na wodę lub paliwo.
.
Dlaczego zostawienie pustej przestrzeni pod szpilką jest tak ważne? Ponieważ musicie zapobiec sytuacji, w której płynna żywica osiądzie na dnie i zostanie ściskana z ogromną siłą przez wkręcaną szpilkę. Nawet przez lekkie pokręcanie śruby drobnozwojnej jesteście w stanie wytworzyć ciśnienie rzędu 250-300 atm. Płynna żywica napotykając nawet niewielką szczelinkę rozerwie materiał.
Tego typu wzmacniacze hydrauliczne stosujemy na przykład w tokarskich uchwytach obróbkowych do bardzo precyzyjnych wałków, w których zwykły uchwyt szczękowy uszkodziłby wcześniej szlifowaną powierzchnie. Wałek taki jest obciskany przez tuleje o podwójnych ściankach pomiędzy którymi znajduje się właśnie tak ściskany olej (a tak naprawdę specjalna zagęszczona masa plastyczna).
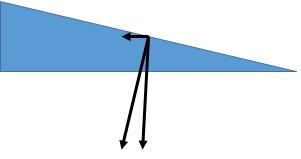
Rysunek 7. Wyjaśnienie, w jaki sposób możemy doprowadzić do rozerwania belki, jeżeli ściśniemy szpilką żywicę na dnie otworu. Pozioma siła pochodzi od naszej ręki wkręcającej szpilkę
Dlaczego zostawienie pustej przestrzeni pod szpilką jest tak ważne? Ponieważ musicie zapobiec sytuacji, w której płynna żywica osiądzie na dnie i zostanie ściskana z ogromną siłą przez wkręcaną szpilkę. Nawet przez lekkie pokręcanie śruby drobnozwojnej jesteście w stanie wytworzyć ciśnienie rzędu 250-300 atm. Płynna żywica napotykając nawet niewielką szczelinkę rozerwie materiał.
Tego typu wzmacniacze hydrauliczne stosujemy na przykład w tokarskich uchwytach obróbkowych do bardzo precyzyjnych wałków, w których zwykły uchwyt szczękowy uszkodziłby wcześniej szlifowaną powierzchnie. Wałek taki jest obciskany przez tuleje o podwójnych ściankach pomiędzy którymi znajduje się właśnie tak ściskany olej (a tak naprawdę specjalna zagęszczona masa plastyczna).
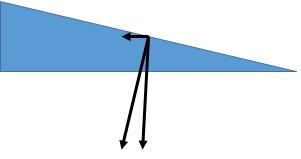
Rysunek 7. Wyjaśnienie, w jaki sposób możemy doprowadzić do rozerwania belki, jeżeli ściśniemy szpilką żywicę na dnie otworu. Pozioma siła pochodzi od naszej ręki wkręcającej szpilkę
.
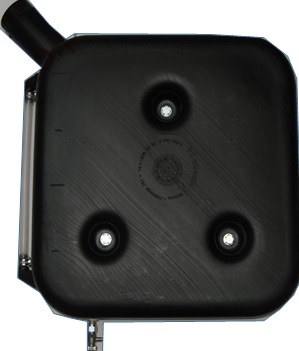
Rysunek 8. Płaski, wygodny w instalacji zbiornik na olej napędowy (od Webasto). Pojemność 12 l.
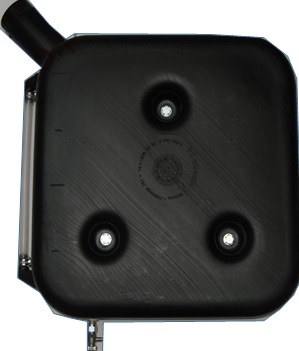
Rysunek 8. Płaski, wygodny w instalacji zbiornik na olej napędowy (od Webasto). Pojemność 12 l.
.
Jeżeli będziemy musieli powiesić płaski zbiornik na grodzi (na przykład standardowy zbiornik od Webasto - rys. 8) to najlepiej jest wykonać z płaskownika pomocniczą ramkę, wspawać w nią szpilki i przykleić od tyłu w paru punktach Sikaflexem konstrukcyjnym (w paru punktach - bo jest drogi i nie ma sensu go zużywać na rzeczy zbędne).
Bez kłopotu można je wieszać na wewnętrznych ściankach bakist. Używane (z ciężarówek) kosztują niewiele, a ich montaż jest zadziwiająco łatwy. Zajmują też bardzo mało miejsca. Przeźroczysta rurka służy do kontroli poziomu paliwa. Rozważcie ich instalacje, jako żelaznej rezerwy paliwowej, uruchamianej kranikiem na dole. Wpięcie w linię paliwową za pomocą trójnika montowanego przed filtrem.
Wracając do głównego tematu wykonania łoża i prostoliniowego spasowania go z osią pochwy. Łoże laminatowe wykonujemy inaczej (ostatnie kilka konstrukcji na Holy śp. Edka Zająca). Oto prosty i szybki sposób. Pokaże to na przykładzie trudnego przypadku, gdy musicie je wylaminować na dużej krzywiźnie kształtującej zęzę na jachtach o pięknej, klasycznej konstrukcji kadłuba. Do wykonania fundamentu musicie zbudować skrzynkę z płyty pilśniowej o wymiarach przyszłego fundamentu. Musi być ona możliwie starannie dopasowana do kadłuba. Mocujemy ją do dna za pomocą srebrnej taśmy.
Przed jej zamocowaniem BARDZO STARANNIE PRZYGOTOWUJEMY KADŁUB W MIEJSCU LAMINOWANIA. Usuwamy z niego wierzchnią warstwę topkotu i szlifujemy, aż uzyskamy jednolitą, szorstką powierzchnię pierwotnego laminatu. Najwygodniej jest to zrobić używając akumulatorowej szlifierki oraz tarcz (ściernic) listkowych o gradacji 40 lub 80.
Ściernice te produkowane są z listków włókniny ściernej przymocowanej do rdzenia wykonanego z włókien szklanych. Nasyp elektrokorundowy (A/O) oraz z węglika krzemu (SiC).
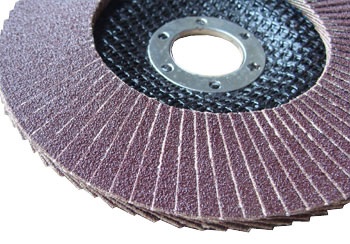
Rysunek 9 Ściernica listkowa
Bez kłopotu można je wieszać na wewnętrznych ściankach bakist. Używane (z ciężarówek) kosztują niewiele, a ich montaż jest zadziwiająco łatwy. Zajmują też bardzo mało miejsca. Przeźroczysta rurka służy do kontroli poziomu paliwa. Rozważcie ich instalacje, jako żelaznej rezerwy paliwowej, uruchamianej kranikiem na dole. Wpięcie w linię paliwową za pomocą trójnika montowanego przed filtrem.
Wracając do głównego tematu wykonania łoża i prostoliniowego spasowania go z osią pochwy. Łoże laminatowe wykonujemy inaczej (ostatnie kilka konstrukcji na Holy śp. Edka Zająca). Oto prosty i szybki sposób. Pokaże to na przykładzie trudnego przypadku, gdy musicie je wylaminować na dużej krzywiźnie kształtującej zęzę na jachtach o pięknej, klasycznej konstrukcji kadłuba. Do wykonania fundamentu musicie zbudować skrzynkę z płyty pilśniowej o wymiarach przyszłego fundamentu. Musi być ona możliwie starannie dopasowana do kadłuba. Mocujemy ją do dna za pomocą srebrnej taśmy.
Przed jej zamocowaniem BARDZO STARANNIE PRZYGOTOWUJEMY KADŁUB W MIEJSCU LAMINOWANIA. Usuwamy z niego wierzchnią warstwę topkotu i szlifujemy, aż uzyskamy jednolitą, szorstką powierzchnię pierwotnego laminatu. Najwygodniej jest to zrobić używając akumulatorowej szlifierki oraz tarcz (ściernic) listkowych o gradacji 40 lub 80.
Ściernice te produkowane są z listków włókniny ściernej przymocowanej do rdzenia wykonanego z włókien szklanych. Nasyp elektrokorundowy (A/O) oraz z węglika krzemu (SiC).
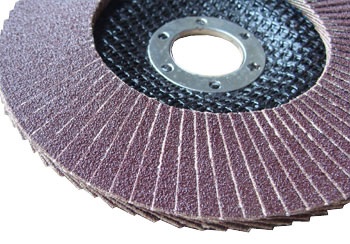
Rysunek 9 Ściernica listkowa
.
Używając ściernicy listkowej nie dociskamy jej zbytnio do szlifowanego laminatu – ziarna tarczy powinny go ścinać, a nie nadtapiać. Praca jest szybka i komfortowa. Znacznie wygodniejsza niż płaskimi tarczami na rzepy.
Mając przygotowaną powierzchnię oraz umocowaną skrzynkę możemy przystąpić do przygotowania laminatu. Może jeszcze jedna uwaga. Górna krawędź skrzynki powinna być zeszlifowana pod takim kątem, jak wynika to z pomiarów przyszłego pochylenia silnika i linii wału (patrz rysunek 4). Sposób wyznaczenia tego kąta opiszemy w następnym artykule. Teraz sposób przygotowania laminatu.

Rysuinek 10. Skrzynka formierska
Używając ściernicy listkowej nie dociskamy jej zbytnio do szlifowanego laminatu – ziarna tarczy powinny go ścinać, a nie nadtapiać. Praca jest szybka i komfortowa. Znacznie wygodniejsza niż płaskimi tarczami na rzepy.
Mając przygotowaną powierzchnię oraz umocowaną skrzynkę możemy przystąpić do przygotowania laminatu. Może jeszcze jedna uwaga. Górna krawędź skrzynki powinna być zeszlifowana pod takim kątem, jak wynika to z pomiarów przyszłego pochylenia silnika i linii wału (patrz rysunek 4). Sposób wyznaczenia tego kąta opiszemy w następnym artykule. Teraz sposób przygotowania laminatu.

Rysuinek 10. Skrzynka formierska
.
Do dużego słoja wlewam Epidian 53 (czyli ten modyfikowany styrenem) oczywiście bez utwardzacza w ilości oczywiście mniejszej niż wynikająca z przewidywanej objętości skrzynki. Następnie tnę tkaninę oraz matę na paski i wrzucam pocięte paski do słoja spokojnie mieszając powstały makaron. Ważne jest aby włókna splątały się ze sobą tworząc przestrzenną, anizotropową konstrukcję. Konsystencja powinna być maksymalnie gęsta. To oznacza, że zbrojenie musi stanowić minimum 60-70% objętości – czym więcej tym lepiej. Warto to robić w słoju, bo możecie wizualnie kontrolować jednorodność mieszaniny. Działa tu reguła kciuka. Dodajecie na przemian zbrojenia i żywicy dopóki roztwór daje się starannie mieszać w całej objętości. Zatem wbrew pozorom wcale nie potrzebujecie bardzo dużo drogiego zestawu EP53+Z1.
Po wymieszaniu zostawiam słój na 45-60 minut, czekając aż rozpuści się do końca proszkowe lepiszcze maty.
W międzyczasie od środka laminuje cienkimi paskami tkaniny krawędzie skrzynki – inaczej ciekła żywica wypłynęła by dołem. Nie ma potrzeby laminowania pionowych krawędzi – tu srebrna taśma będzie wystarczająca. Oczywiście, jeżeli mamy przydatne elementy kadłuba (na przykład laminatowe denniki), to wykorzystujemy je rezygnując z wybranych ścianek skrzynki.
Samo laminowanie jest proste i szybkie. Pobieramy ze słoja porcję roztworu (optymalnie 200-400 ml – ale raczej nie więcej) i dodajemy stosowną ilość utwardzacza. Mieszamy starannie, a następnie łopatką przenosimy laminat do skrzynki, warstwa po warstwie, czekając aż się równo wypełni skrzynkę. Może być potrzebny krótko przycięty pędzel, gdyż pomaga usunąć pęcherzyki powietrza. To ważne. Między innymi z powodu pęcherzyków nie powinniśmy nakładać zbyt dużej ilości roztworu na raz, pamiętając, że żelowaniu żywicy towarzyszy wydzielanie ciepła. Ostatnią warstwę nanosimy fragmentami budując skos poprzez pozwolenie na częściowe zastyganie mieszaniny z pewnym naddatkiem. W końcowej warstwie wyrównujemy szpachelką z poliamidu wierzchnią warstwę wykorzystując krawędzie skrzynki jako wzorniki.
Po upływie dwóch dób fundament jest już gotów (80-90% wytrzymałości). Faktycznie mając nóż na gardle w remoncie roztrzaskanej na nabrzeżu Holy Marek Wąsik wykonał kolejną wersję fundamentu z prędkością światła, co oznaczało, że w 7-8 godzinach zapalaliśmy osadzony na nim silnik, który udało mi się zreanimować po spędzeniu przez niego nocy na dnie Basenu Węglowego w Ustce. Poszło wtedy sporo drogiego utwardzacza.
Ale Państwo spokojnie demontujecie swoje skrzynki po zastygnięciu laminatu i oczom ukazuje się piękna, mocna i gładka konstrukcja. Zazwyczaj wymaga drobnego przeszlifowania – rzadko szpachlowania (ale to nie są tony pyłu) i nie musimy kielnią nanosić szpachlówki.
Całość wykończamy specjalną farbą do zęz pamiętając oczywiście o użyciu właściwego primera – o ile zaleca to producent farby (patrz przypis na dole).
Na koniec wiercimy i gwintujemy otwory pod drobnozwojowe szpilki i wkręcamy je na Epidian. Szpilki te posłużą albo umocowaniu stalowej płytki pośredniej (w wariancie gdy szpilki będą w nią wkręcane – jak u mnie na Donaldzie) albo posłużą bezpośredniemu mocowaniu poduszek, gdy mają one swoje własne łapy (jak na przykład w poduszkach od Opla).
Aha, nie jestem fanem wlaminowywania w fundament stalowych elementów mocujących (płaskowników). Lepszym rozwiązaniem wydaje mi się ich naklejenie na Sikaflex i dociągnięcie szpilkami. Jeżeli trzeba będzie wymienić płaskownik z dowolnego powodu (na przykład, aby dospawać do niego coś nowego) to jego demontaż nie będzie problemem. Mam też wrażenie, że taka przekładka wibroizolacyjna wiele daje.
Zamykając temat laminatowego fundamentu. Zwróćcie uwagę, że proponuje wykonanie go jako konstrukcji monolitycznej, a nie skrzynkowej. Są za tym trzy argumenty. Pierwszy dotyczy łatwości i pewności osadzenia szpilek. Fundament i mocowanie musi być bardzo solidne. Zdarzyło mi się nie raz i nie dwa, że uderzony szkwałem 50 stopowy jacht idący na silniku pod maleńkim, sztormowym fokiem stabilizującym potrafił się niemal położyć masztem na wodzie (raz się położył). Wyobraźcie sobie jak duże obciążenie rozciągające musi wtedy przenieść górny fragment łoża!
Argumentem drugim jest to, że od zawsze czułem awersję do konstruowania pustych kesonów konstrukcyjnych z laminatu poddanym zmiennym, punktowym obciążeniom. Teoretycznie laminat powinien być jednorodny. Ale teoria nie pokrywa się tutaj z jego rozwarstwieniami obserwowanym na przykład w miejscu mocowania knag cumowniczych, pantografów lub łożysk oporowych wału silnika. A nie sądzę, aby wszyscy szkutnicy popełnili tu błędy. Dla hobbystów ciekawy artykuł z Instytutu Lotnictwa http://ilot.edu.pl/prace_ilot/public/PDF/spis_zeszytow/221_2011/02.%20Czajkowska%20K.,%20Szel%C4%85g%20D.,%20Lorenc%20Z.,%20Czarnocki%20P..pdf
Argument trzeci uzasadnia przekonywująco rysunek 11.
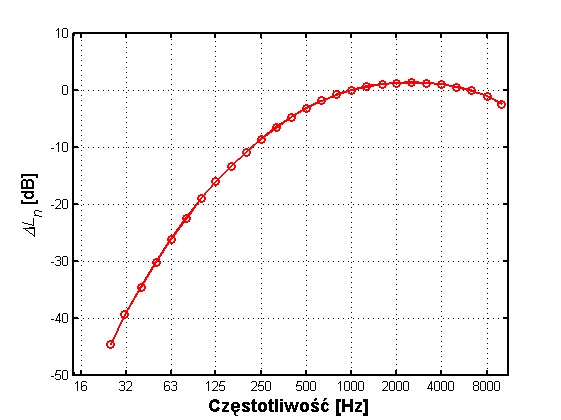
Rysunek 11. Krzywa korekcyjna ucha ludzkiego, pokazująca zależność czułości ucha od częstotliwości dźwięku
Po wymieszaniu zostawiam słój na 45-60 minut, czekając aż rozpuści się do końca proszkowe lepiszcze maty.
W międzyczasie od środka laminuje cienkimi paskami tkaniny krawędzie skrzynki – inaczej ciekła żywica wypłynęła by dołem. Nie ma potrzeby laminowania pionowych krawędzi – tu srebrna taśma będzie wystarczająca. Oczywiście, jeżeli mamy przydatne elementy kadłuba (na przykład laminatowe denniki), to wykorzystujemy je rezygnując z wybranych ścianek skrzynki.
Samo laminowanie jest proste i szybkie. Pobieramy ze słoja porcję roztworu (optymalnie 200-400 ml – ale raczej nie więcej) i dodajemy stosowną ilość utwardzacza. Mieszamy starannie, a następnie łopatką przenosimy laminat do skrzynki, warstwa po warstwie, czekając aż się równo wypełni skrzynkę. Może być potrzebny krótko przycięty pędzel, gdyż pomaga usunąć pęcherzyki powietrza. To ważne. Między innymi z powodu pęcherzyków nie powinniśmy nakładać zbyt dużej ilości roztworu na raz, pamiętając, że żelowaniu żywicy towarzyszy wydzielanie ciepła. Ostatnią warstwę nanosimy fragmentami budując skos poprzez pozwolenie na częściowe zastyganie mieszaniny z pewnym naddatkiem. W końcowej warstwie wyrównujemy szpachelką z poliamidu wierzchnią warstwę wykorzystując krawędzie skrzynki jako wzorniki.
Po upływie dwóch dób fundament jest już gotów (80-90% wytrzymałości). Faktycznie mając nóż na gardle w remoncie roztrzaskanej na nabrzeżu Holy Marek Wąsik wykonał kolejną wersję fundamentu z prędkością światła, co oznaczało, że w 7-8 godzinach zapalaliśmy osadzony na nim silnik, który udało mi się zreanimować po spędzeniu przez niego nocy na dnie Basenu Węglowego w Ustce. Poszło wtedy sporo drogiego utwardzacza.
Ale Państwo spokojnie demontujecie swoje skrzynki po zastygnięciu laminatu i oczom ukazuje się piękna, mocna i gładka konstrukcja. Zazwyczaj wymaga drobnego przeszlifowania – rzadko szpachlowania (ale to nie są tony pyłu) i nie musimy kielnią nanosić szpachlówki.
Całość wykończamy specjalną farbą do zęz pamiętając oczywiście o użyciu właściwego primera – o ile zaleca to producent farby (patrz przypis na dole).
Na koniec wiercimy i gwintujemy otwory pod drobnozwojowe szpilki i wkręcamy je na Epidian. Szpilki te posłużą albo umocowaniu stalowej płytki pośredniej (w wariancie gdy szpilki będą w nią wkręcane – jak u mnie na Donaldzie) albo posłużą bezpośredniemu mocowaniu poduszek, gdy mają one swoje własne łapy (jak na przykład w poduszkach od Opla).
Aha, nie jestem fanem wlaminowywania w fundament stalowych elementów mocujących (płaskowników). Lepszym rozwiązaniem wydaje mi się ich naklejenie na Sikaflex i dociągnięcie szpilkami. Jeżeli trzeba będzie wymienić płaskownik z dowolnego powodu (na przykład, aby dospawać do niego coś nowego) to jego demontaż nie będzie problemem. Mam też wrażenie, że taka przekładka wibroizolacyjna wiele daje.
Zamykając temat laminatowego fundamentu. Zwróćcie uwagę, że proponuje wykonanie go jako konstrukcji monolitycznej, a nie skrzynkowej. Są za tym trzy argumenty. Pierwszy dotyczy łatwości i pewności osadzenia szpilek. Fundament i mocowanie musi być bardzo solidne. Zdarzyło mi się nie raz i nie dwa, że uderzony szkwałem 50 stopowy jacht idący na silniku pod maleńkim, sztormowym fokiem stabilizującym potrafił się niemal położyć masztem na wodzie (raz się położył). Wyobraźcie sobie jak duże obciążenie rozciągające musi wtedy przenieść górny fragment łoża!
Argumentem drugim jest to, że od zawsze czułem awersję do konstruowania pustych kesonów konstrukcyjnych z laminatu poddanym zmiennym, punktowym obciążeniom. Teoretycznie laminat powinien być jednorodny. Ale teoria nie pokrywa się tutaj z jego rozwarstwieniami obserwowanym na przykład w miejscu mocowania knag cumowniczych, pantografów lub łożysk oporowych wału silnika. A nie sądzę, aby wszyscy szkutnicy popełnili tu błędy. Dla hobbystów ciekawy artykuł z Instytutu Lotnictwa http://ilot.edu.pl/prace_ilot/public/PDF/spis_zeszytow/221_2011/02.%20Czajkowska%20K.,%20Szel%C4%85g%20D.,%20Lorenc%20Z.,%20Czarnocki%20P..pdf
Argument trzeci uzasadnia przekonywująco rysunek 11.
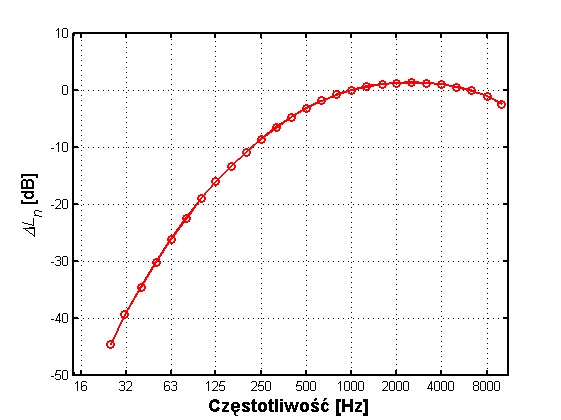
Rysunek 11. Krzywa korekcyjna ucha ludzkiego, pokazująca zależność czułości ucha od częstotliwości dźwięku
.
Pełny fundament, solidnie zintegrowany z kadłubem drga wtórnie z niższymi częstotliwościami (praktyka). A więc hałas wtórny we wnętrzu jest przy tej samej mocy odbierany przez ucho jako subiektywnie istotnie mniejszy. Dlatego też, jak sobie przypominacie, projektując kolektor do marynizowanego silnika, dążyłem do uzyskania w puszce rozprężnej możliwie dużej objętości dającej na wolnych obrotach przyjemny, basowy pomruk, nie zakłócający prowadzonych w kokpicie półgłosem rozmów. Jeżeli już musicie wykonać keson – wypełnijcie go twardą pianką głuszącą.
W następnym odcinku – precyzyjne wytyczenie osi wału i osadzenie pochwy w kadłubie, a także o uszczelnieniu przednimi.
Pozdrawiam cały klan SSI
T.L.
Pełny fundament, solidnie zintegrowany z kadłubem drga wtórnie z niższymi częstotliwościami (praktyka). A więc hałas wtórny we wnętrzu jest przy tej samej mocy odbierany przez ucho jako subiektywnie istotnie mniejszy. Dlatego też, jak sobie przypominacie, projektując kolektor do marynizowanego silnika, dążyłem do uzyskania w puszce rozprężnej możliwie dużej objętości dającej na wolnych obrotach przyjemny, basowy pomruk, nie zakłócający prowadzonych w kokpicie półgłosem rozmów. Jeżeli już musicie wykonać keson – wypełnijcie go twardą pianką głuszącą.
W następnym odcinku – precyzyjne wytyczenie osi wału i osadzenie pochwy w kadłubie, a także o uszczelnieniu przednimi.
Pozdrawiam cały klan SSI
T.L.
-------------------------------
PS. Aby dać pewne wyobrażenie o cenach materiałów i ich bardziej szczegółowych opisach załączam linki od naszego kolegi ze Szczecina, Pawła Ryżewskiego. Podane ceny są dobrą referencją, a reputacja firmy w moich oczach jest nienaganna. Praktycznie cała chemia wmalowana lub wlepiona w "Donalda" pochodzi od tego dostawcy. Jakby co – dzwońcie do Pawła po radę, numery znajdziecie na podanych stronach.
Do laminowania żywica epoksydowa Epidian 53:
http://www.farbyjachtowe.pl/epidian-53-modyfikowana-styrenem-zywica-epoksydowa-1kg-p-610.html
Z utwardzaczem Z1
http://www.farbyjachtowe.pl/utwardzacz-z1-do-cieklych-zywic-epoksydowych-kg-p-626.html
Tkanina szklana 200 - 400 g/m2
http://www.farbyjachtowe.pl/tkanina-szklana-200-1m2-p-192.html
Mata szklana do epoksydów (lepiszcze proszkowe) gramatura jak tkanina.
http://www.farbyjachtowe.pl/mata-szklana-1m2-gramatura-150-lub-300-p-190.html
Farba do zęzy dwuskładnikowa:
http://www.farbyjachtowe.pl/farba-podkladowa-epoksydowa-epoxy-primer-075l-p-9.html
albo
http://www.farbyjachtowe.pl/farba-podkladowa-epoksydowa-uniwersalna-117-mulitipurpose-epoxy-primer-1l-p-182.html
System jednoskładnikowy:
Podkład
http://www.farbyjachtowe.pl/farba-podkladowa-uniwersalna-multi-marine-primer-075l-p-48.html
Nawierzchniowa
http://www.farbyjachtowe.pl/farba-ochronna-do-zez-bakist-komor-silnika-itp-bilge-paint-075-p-24.html
PS. Aby dać pewne wyobrażenie o cenach materiałów i ich bardziej szczegółowych opisach załączam linki od naszego kolegi ze Szczecina, Pawła Ryżewskiego. Podane ceny są dobrą referencją, a reputacja firmy w moich oczach jest nienaganna. Praktycznie cała chemia wmalowana lub wlepiona w "Donalda" pochodzi od tego dostawcy. Jakby co – dzwońcie do Pawła po radę, numery znajdziecie na podanych stronach.
Do laminowania żywica epoksydowa Epidian 53:
http://www.farbyjachtowe.pl/epidian-53-modyfikowana-styrenem-zywica-epoksydowa-1kg-p-610.html
Z utwardzaczem Z1
http://www.farbyjachtowe.pl/utwardzacz-z1-do-cieklych-zywic-epoksydowych-kg-p-626.html
Tkanina szklana 200 - 400 g/m2
http://www.farbyjachtowe.pl/tkanina-szklana-200-1m2-p-192.html
Mata szklana do epoksydów (lepiszcze proszkowe) gramatura jak tkanina.
http://www.farbyjachtowe.pl/mata-szklana-1m2-gramatura-150-lub-300-p-190.html
Farba do zęzy dwuskładnikowa:
http://www.farbyjachtowe.pl/farba-podkladowa-epoksydowa-epoxy-primer-075l-p-9.html
albo
http://www.farbyjachtowe.pl/farba-podkladowa-epoksydowa-uniwersalna-117-mulitipurpose-epoxy-primer-1l-p-182.html
System jednoskładnikowy:
Podkład
http://www.farbyjachtowe.pl/farba-podkladowa-uniwersalna-multi-marine-primer-075l-p-48.html
Nawierzchniowa
http://www.farbyjachtowe.pl/farba-ochronna-do-zez-bakist-komor-silnika-itp-bilge-paint-075-p-24.html
////////////////////////////////////////////////////////////////////////////////////////////////////////////////////////////////////////////////////////////////////////////////////////////
Rysunek do komentarza poniżej:
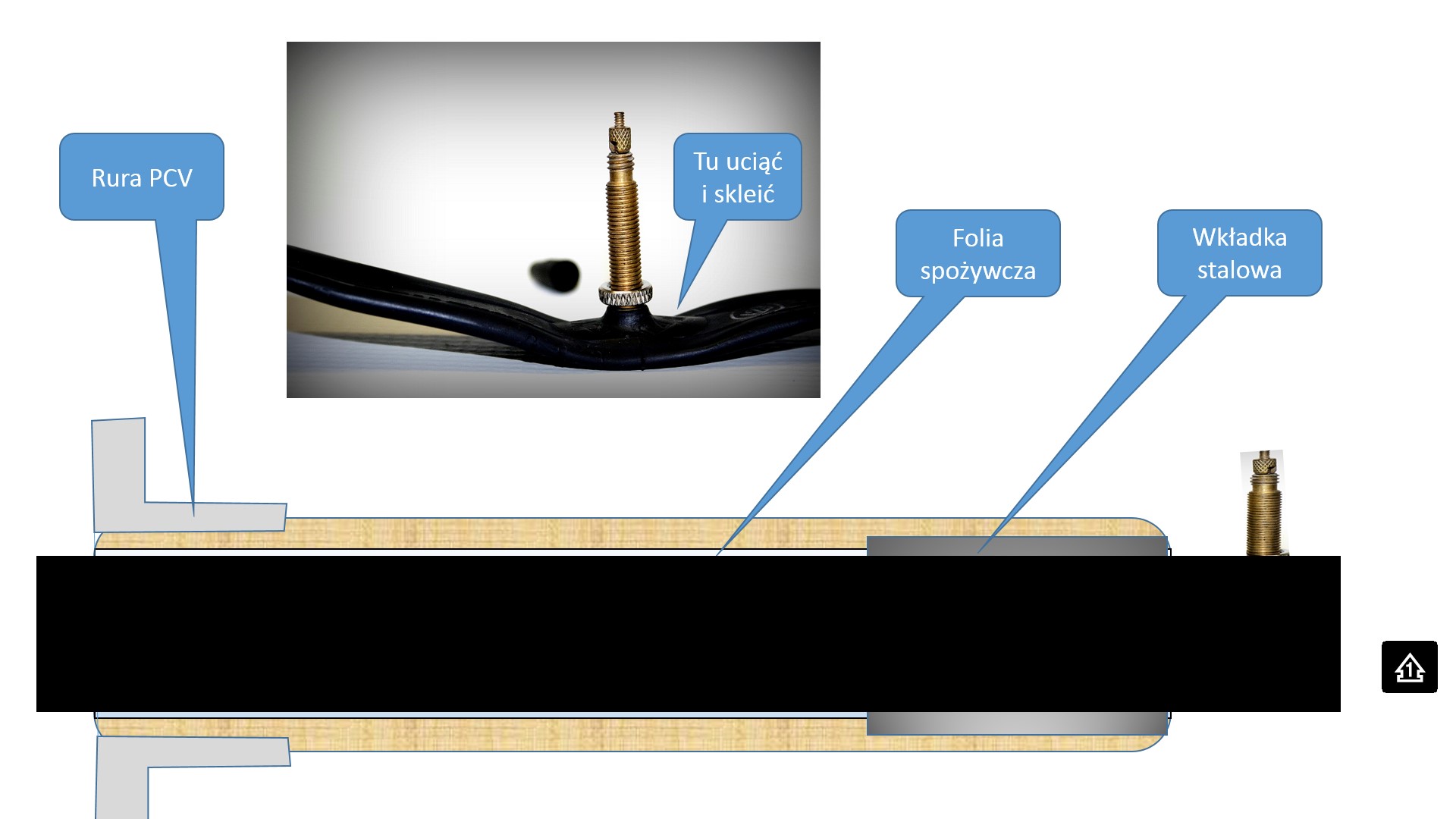
--------------------------------------------------------------------------------------------------------------------
Pytanie Czytelnika SSI:
Panie Tadeuszu,
Wydaje mi się to nieco drogo, zwłaszcza, że i tak czekają mnie prace laminarskie. Czy mógłbym wykonać nadlaminowanie stępki tak jak Pan opisał konstrukcję łoża, a potem go wiercić (czekam z niecierpliwością na następny artykuł!).
I tak kupiłem już tkaninę i żywicę.
Odpowiedź:
Panie Tomku,
Oto najprostsza, sprawdzona technologia:
Kupuje Pan dętkę rowerową (z roweru kolarskiego – czyli tę z cieńszych). Rozcina Pan ją tuż za zaworem i skleja (może być na gorąco u wulkanizatora albo zwykłym klejem do gumy. Skleja Pan też drugi koniec (rys.1).
Pompuje Pan do pożądanej średnicy wewnętrznej wału nakładając z jednego końca stalową tuleję dopasowaną wymiarem wewnętrznym do łożyska metalowo-gumowego (zewnętrzna powierzchnia musi być podrapana szczotką stalową oraz starannie odłuszczona acetonem).
Dętka powinna być napompowana do średnicy docelowej D-4 mm (czyli po 2 mm na stronę). Owijamy dętkę cienką folią spożywczą (z rolki – 1,15 zł za rolkę 20 mb – wystarczy). Oczywiście nie owijając obudowy łożyska tylnego.
Dopompowujemy do średnicy nominalnej. Folia się rozciągnęła i wygładziła. Ma Pan idealnie gładki, twardy rdzeń rury.
Teraz laminuje Pan ją diagonalnie. Wystarczy 6-8 warstw (po cztery krzyżowo w każdym z kierunków). Laminujemy „mokre na mokre”. Zejdzie na to to około 2 godzin.
TRICK. Jeżeli macie na warsztacie kawałek gładkiej płyty pilśniowej, to praca pójdzie błyskawicznie, jeżeli będziecie toczyć laminowaną rurę w tę i z powrotem.
Gdy skończy Pan prace proszę nasunąć na przedni koniec kawałek rury z PCW wysmarowanej od środka pastą do podłogi (lub bezbarwną do butów) o średnicy wewnętrznej takiej, jak planowana średnica wewnętrzna rury gumowej łączącej pochwę z dławicą przednią.
Wiesza Pan ją do przeschnięcia pionowo. Po okresie około 1 doby (dla EP53+Z1) pochwa jest gotowa. Zdejmuje Pan rurę z PCW spuszcza powietrze z dętki. Zagląda Pan z zachwytem do środka idealnie gładkiej, równiej i lśniącej rury.
Teraz tylko otwór w kadłubie i laminujemy ją z zewnątrz i wewnątrz. Całość pochłonie około 4 godzin niespiesznej pracy (można to zrobić szybciej – ale musiałby Pan kupić taśmę w rolce i odwijać ją z zaimprowizowanego kołowrotka powieszonego na drucie nad warsztatem.
Koszt materiałów dla pochwy 1000-1200 mm to około 150-200 zł. Czyli uzyskał Pan stawkę za swoją pracę (3400-200)/4 = 800 zł/h
Powodzenia! Proszę do Jurka przysłać zdjęcia.
Pozdrawiam. Tadeusz Lis
PS. Proszę nie wyrzucać dętki. Przyda się do wylaminowania na przykład krzywoliniowego wprowadzenia do łańcucha kotwicznego lub przepustów grodziowych rury gumowej wyd