KOLEKTOR CHŁODZONY CIECZĄ (4)
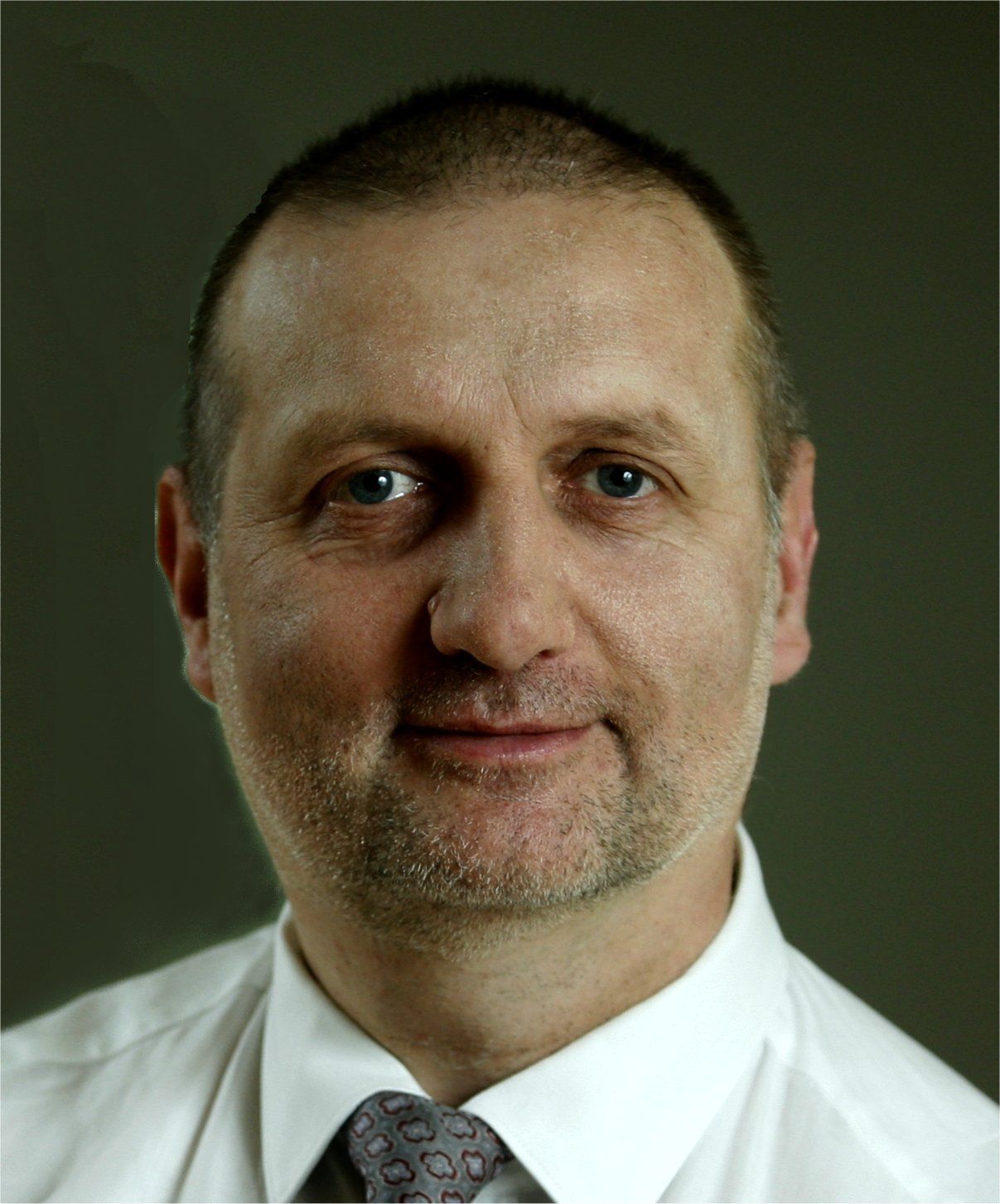
Autor jest przywalony mailami i telefonami. Dlatego zapytania proszę przysyłać do SSI w celu dokonania pogrupowania tematycznego.
Tadeusz Lis będzie odpowiadał wszystkim, ale "w blokach".
Cały czas myślimy o grubej, papierowej książce poradnikowej, którą wyda oczywiście .. "NOWATOR" Kartuzy.
Podsuwajcie tematy, które uznacie jako ważne i powszechnie interesujące.
Żyjcie wiecznie !
Don Jorge
________________________
Budujemy prosty kolektor chłodzony cieczą.
Niniejszy artykuł jest odpowiedzią na prośbę Kolegi Arka o poglądowe rysunki opisanego wcześniej kolektora oraz wskazówki wykonawcze.
Nie podaje dokładnych wymiarów, gdyż zależą one od konkretnego silnika – ważne są proporcję oraz zachowanie właściwej geometrii.
Sugeruje, aby zainteresowani Koledzy wykonali swoje kolektory dokładnie według poniższych wskazówek. Projektując te rozwiązanie starałem się tak opracować technologię, aby uzyskać finalny rezultat w możliwie małej ilości ruchów.
Sugerowałbym, aby poważnie rozważyć wykonanie wszystkich ścianek z użyciem technologii cięcia laserem lub wodą pod ciśnieniem. Ceny tych usług bardzo staniały w Polsce. Jednak moje doświadczenie pokazuje, że rozrzut cenowy jest bardzo duży i zakład w małej miejscowości potrafi być 6 razy tańszy niż w Warszawie.
Zlecając wycięcie elementów kolektora musicie dostarczyć ich rysunki – najlepiej w formacie AutoCAD’a. Ale jeżeli jest to poza zasięgiem Waszych możliwości, to dostarczenie ich w postaci odręcznych, zwymiarowanych szkiców nie podnosi dramatycznie ceny usługi.
Poniżej wariant wykonania przy użyciu klasycznych narzędzi i maszyn – przy założeniu, że dla obniżenia kosztu maksimum prac wykonacie własnoręcznie.
Pracę zaczynamy od wytrasowania płyty mocującej kolektor do głowicy. Jej grubość powinna wynosić około 8 mm – musi być sztywna (rys. 8). Wycinamy ją
Następnie na blasze grubości 2.5 do 3 mm trasujemy elementy zewnętrznego płaszcza nr 6, 7, 8, 9 zauważając, że mają one taką samą szerokość. A więc będziecie mieli jedną, prostą linię cięcia. Potem trasujecie i wycinacie ściankę przednią płaszcza (nr 10) zauważając, że jest wymiarowo identyczna jak ścianka płyty głównej.
W następnym kroku z pozostałej blachy wycinacie ścianki wewnętrznej komory 1,2, 3, 4 – znów mają one taką samą szerokość – a więc jedno proste cięcie, z jednego zamocowania. Pozostała nam tylko ścianka zamykająca nr 5. Trasując ją na blasze zauważamy, że długość jej boku jest identyczna jak 1, 4 – oszczędzacie blachę oraz długość cięcia.
Blachę tej grubości łatwo tnie się w warunkach garażowych tarczą szlifierską. Macie już gotowe elementy, teraz czeka Was wycieczka do najbliższego warsztatu ślusarskiego, aby wykonać niezbędne otwory. W pierwszej kolejności trasujecie otwory w głównej płycie mocującej. Są to otwory wydechowe oraz tulejek przez które przejdą śruby mocujące (rysunek 1). Pełnią one dodatkową funkcję polepszając mieszanie spalin w komorze rozprężnej – są odpowiednikiem przegród w samochodowych tłumikach refleksyjnych (nie absorbcyjnych). Tulejki powinny mieć luz 2-3 mm w stosunku do śruby mocującej (lepiej 2 mm – jeżeli jesteście pewni dokładności trasowania rozstawu otworów).
Niniejszy artykuł jest odpowiedzią na prośbę Kolegi Arka o poglądowe rysunki opisanego wcześniej kolektora oraz wskazówki wykonawcze.
Nie podaje dokładnych wymiarów, gdyż zależą one od konkretnego silnika – ważne są proporcję oraz zachowanie właściwej geometrii.
Sugeruje, aby zainteresowani Koledzy wykonali swoje kolektory dokładnie według poniższych wskazówek. Projektując te rozwiązanie starałem się tak opracować technologię, aby uzyskać finalny rezultat w możliwie małej ilości ruchów.
Sugerowałbym, aby poważnie rozważyć wykonanie wszystkich ścianek z użyciem technologii cięcia laserem lub wodą pod ciśnieniem. Ceny tych usług bardzo staniały w Polsce. Jednak moje doświadczenie pokazuje, że rozrzut cenowy jest bardzo duży i zakład w małej miejscowości potrafi być 6 razy tańszy niż w Warszawie.
Zlecając wycięcie elementów kolektora musicie dostarczyć ich rysunki – najlepiej w formacie AutoCAD’a. Ale jeżeli jest to poza zasięgiem Waszych możliwości, to dostarczenie ich w postaci odręcznych, zwymiarowanych szkiców nie podnosi dramatycznie ceny usługi.
Poniżej wariant wykonania przy użyciu klasycznych narzędzi i maszyn – przy założeniu, że dla obniżenia kosztu maksimum prac wykonacie własnoręcznie.
Pracę zaczynamy od wytrasowania płyty mocującej kolektor do głowicy. Jej grubość powinna wynosić około 8 mm – musi być sztywna (rys. 8). Wycinamy ją
Następnie na blasze grubości 2.5 do 3 mm trasujemy elementy zewnętrznego płaszcza nr 6, 7, 8, 9 zauważając, że mają one taką samą szerokość. A więc będziecie mieli jedną, prostą linię cięcia. Potem trasujecie i wycinacie ściankę przednią płaszcza (nr 10) zauważając, że jest wymiarowo identyczna jak ścianka płyty głównej.
W następnym kroku z pozostałej blachy wycinacie ścianki wewnętrznej komory 1,2, 3, 4 – znów mają one taką samą szerokość – a więc jedno proste cięcie, z jednego zamocowania. Pozostała nam tylko ścianka zamykająca nr 5. Trasując ją na blasze zauważamy, że długość jej boku jest identyczna jak 1, 4 – oszczędzacie blachę oraz długość cięcia.
Blachę tej grubości łatwo tnie się w warunkach garażowych tarczą szlifierską. Macie już gotowe elementy, teraz czeka Was wycieczka do najbliższego warsztatu ślusarskiego, aby wykonać niezbędne otwory. W pierwszej kolejności trasujecie otwory w głównej płycie mocującej. Są to otwory wydechowe oraz tulejek przez które przejdą śruby mocujące (rysunek 1). Pełnią one dodatkową funkcję polepszając mieszanie spalin w komorze rozprężnej – są odpowiednikiem przegród w samochodowych tłumikach refleksyjnych (nie absorbcyjnych). Tulejki powinny mieć luz 2-3 mm w stosunku do śruby mocującej (lepiej 2 mm – jeżeli jesteście pewni dokładności trasowania rozstawu otworów).

Wytrasowanie otworów jest bardzo łatwe – jeżeli dysponujecie starym, zdjętym kolektorem (patrz artykuł wcześniejszy o kupowaniu silnika (http://www.kulinski.navsim.pl/art.php?id=2329&page=0 ). Jeżeli wydaje Wam się to trudne – to po prostu zanieście kolektor frezerowi, który wykona dla Was otwory w płytach.
Jeżeli jednak zdecydujecie się na samodzielne wiercenie otworów na wiertarce stołowej którą macie w garażu, to sugeruję następującą kolejność:
a. Najpierw główna płyta nośna
b. Potem w złożeniu, traktując płytę, jako płytę wiertarską wiercimy otwory do osadzenia tulejek w przedniej ściance komory rozprężnej oraz w przedniej ściance płaszcza wodnego (nr 10 i 5 na rysunku 8)
c. Jeżeli mamy wiertarkę odpowiedniej mocy, to nie powinno być (w przypadku opisywanego silnika d722) z wykonaniem otworów spalinowych – ich średnica o ile dobrze pamiętam wynosi 20 mm.
Jeżeli macie w przydomowym warsztacie nawet małą tokarkę z uchwytem czteroszczękowym, to nie powinno być kłopotu z wytoczeniem otworów dla rury wydechowej. Najlepiej jest je oczywiście wytoczyć w złożeniu. Jeżeli macie tylko uchwyt trójszczękowy to też można to zrobić stosując następujący trick warsztatowy:
a. Wytrasujcie i wywierćcie na płytkach numer 3 i 7 otwór pilotowy fi=15 mm.
b. Dospawajcie (pachwinowo) właściwą rurę wydechową do blachy nr 3 centrując ją wokół otworu
c. Sczepcie (heftnijcie) spawarką w paru punktach blachę nr 3 oraz 7
d. Zamocujcie w uchwycie trójszczękowym obie blachy wykorzystując do tego dospawaną rurę – zapewni Wam idealne wycentrowanie otworu wylotowego
e. Roztoczcie w obu blachach otwór fi=15 do właściwej średnicy wewnętrznej rury wydechowej (zwykle około 40-50 mm)
f. Szlifierką obetnijcie spawy szczepiające płytki i rozdzielcie je
Macie już wszystkie gotowe elementy. Trzeba tylko jeszcze dociąć tulejki. Grubość ich ścianek powinna wynosić 2.5 mm, a długość wynika z zaprojektowanej przez Was szerokości płaszcza powiększona o 3 mm – tyle powinna tulejka wystawać na zewnątrz płaszcza.
Teraz proponuje pospawać elementy w następującej kolejności:
a. Najpierw wspawujemy wszystkie rurki w główną płytę mocującą. Spawamy je od strony bloku silnika. Jeżeli nie macie dużej wprawy w spawaniu ułatwicie sobie życie sfazowując wiertłem krawędzie otworów, aby uzyskać lepszy przetop (ja tak robię). Doświadczonemu spawaczowi nie jest to potrzebne.
b. W następnym kroku spawacie prostopadłe ścianki nr 2 oraz 3.
c. Teraz zanim zamknięcie komorę rozprężną obspawujecie rurki zewnętrznie na ściance nr 5. Dostęp jest dobry – to prosty, zewnętrzny spaw pachwinowy, trudno jest coś popsuć
d. Kolejny spawy krawędziowe połączą ściankę nr 5 ze ściankami 1 i 4. Komora rozprężna jest już zamknięta. Spawacie dalej? Nie – teraz czas na próbę szczelności.
Próba szczelności.
a. Zdejmujecie z silnika nienaruszoną uszczelkę i zakładacie ją na tył kolektora. Z tworzywa sztucznego (kupcie plastikową tackę do krojenia chleba) zrobicie zaślepkę otworów wlotowych przykręcając ją śrubami, które docelowo będą mocowały kolektor
b. W tym samym sklepie, w którym kupiliście tackę kupcie gumowy korek do wanny lub słoja z winem dopasowany średnicą do rury wydechowej
c. Przez otwór w korku podajecie sprężone powietrze z kompresora lub pompki rowerowej
d. Kolektor macie zanurzony w misce lub wanience. Najmniejsze pęcherzyki powietrza na spawie – poprawiamy je do skutku, ponieważ potem nie będziecie mieli już dostępu do komory rozprężnej. Chociaż mówiąc szczerze, jeżeli spawy kładzie doświadczony fachowiec to prawdopodobieństwo nieszczelności jest bliskie zeru. Czasami, rzadko, niespodzianki zdarzają się początkującym spawaczom zwłaszcza przy pracy elektrodą otuloną – a nie TIG-iem.
e. Mamy pewną komorę rozprężną. Teraz spawamy ścianki 6, 7, 8, 9, 10 i oczywiście na ściance nr 10 obspawujemy (znów zewnętrznie) tuleje śrub mocujących. Jest to łatwe, bo zadbaliście o to, aby wystawały 3 mm nad powierzchnię ścianki.
f. Teraz nałożycie na nie podkładki pod nakrętki o grubości 3 mm i przyspawacie je wokół rurek. Dzięki nim mocno dociągnięte śruby (lub nakrętki, jeżeli osadzicie w bloku szpilki) dość dobrze przeniosą obciążenia na zewnętrzną ściankę płaszcza wodnego.
g. W ostatnim kroku obspawujecie rurę wydechową (ścianka nr 7) i wspawujecie w płaszcz rurki wprowadzające i wyprowadzające morską wodę chłodzącą. Specjalnie nie podaje ich położenia, bo to wynika z konkretnej geometrii Waszej przestrzeni podkokpitowej – czyli sposobu w jakim poprowadzicie węże od wymiennika wody chłodzącej (patrz następny odcinek)
Na zakończenie kilka istotnych szczegółów konstrukcyjnych które pokazałem na rysunkach. I tak:
a. Zwróćcie uwagę (rys. 2), aby średnice otworów pod tulejki wykonać tak, aby w główną płytę weszły z lekkim ściskiem – nie będzie Wam trudno pospawać całość w pojedynkę. Ważne jest też, aby średnica otworów wydechowych była identyczna jak w bloku – dzięki temu będziecie mieli gładkie przejście na którym nie będzie odkładał się nagar.
b. Otwór dla rury wydechowej (rys. 3) wykonajcie możliwie jak najbliżej górnej krawędzi komory rozprężnej. Czym jest wyżej, tym mniejsze prawdopodobieństwo dostania się wody do środka komory rozprężnej
c. Na rysunku nr 4 pokazałem jak wspawać pierwszy odcinek rury wydechowej. Jej średnica zewnętrzna powinna być dopasowana do średnicy miękkiego węża, którym doprowadzicie spaliny do zamka wodnego. Węże firmy Vetus, które używałem mają oznaczenie SLANGx, gdzie x jest średnicą rury. Czyli SLANG50 to wąż fi=40 o średnicy wewnętrznej 40 mm – i taką rurę dobierzecie jako wyprowadzenie spalin z kolektora (http://viewer.zmags.com/publication/b84dd7ea#/b84dd7ea/84 strona 84)
d. Ponieważ promień gięcia tych węży nie jest duży, powinniście zejść w dół kolanem hamburskim, tak jak to pokazałem na rysunku 6. Rurkę wtryskową wody (sklepaną na końcu) wspawujemy pionowo. Dzięki temu po wyłączeniu silnika resztka wody spłynie grawitacyjnie do zamka wodnego (blokady wodnej). Unikajcie pozornie prostych rozwiązań jak u nieszczęśnika Andrzeja Ch. – patrz poprzednie artykuły, ponieważ jest to naturalna droga do nienaprawialnych uszkodzeń silnika
e. Na rysunku 5 pokazałem jak jest skonstruowany płaszcz wodny. To co jest ważne, to to, aby odległość pomiędzy ściankami nie była mniejsza niż 10 mm (z praktyki). Wtedy pojemność wody w zładzie jest na tyle duża, że udaje się utrzymać chłodne ścianki zewnętrzne i co ważniejsze – nie występuje zjawisko odkładania się soli. Pamiętajcie jednak, że mimo to, dobra praktyka morska nakazuje, aby na koniec sezonu przepłukać cały układ słodką wodą.
f. Na rysunku 7 podałem Wam wymiary ograniczające wielkość zewnętrzną kolektora (praktyka). Ograniczenia wynikają z:
a. Możliwości dokręcenia przewodu (+) alternatora i dostatecznej przestrzeni dla wypływu powietrza chłodzącego alternator
b. Możliwości odkręcenia tylnej śruby mocującej kołnierz rozrusznika (nasadowym kluczem z grzechotką o drobnych zębach)
c. Możliwości dociągnięcia nakrętek kontrujących śruby regulujące luz popychaczy zaworowych.
g. Projektując wielkość odległości ścianki komory rozprężnej należy przyjąć, że nie powinna być ona mniejsza niż 2.5x otwór wylotowy spalin. Czyli dla średnicy w głowicy rzędu 20 mm powinno to być 50 mm. Oczywiście im puszka większa tym lepiej dla pracy silnika (patrz skutki dla silnika, gdy ten warunek nie jest spełniony – konstrukcja Andrzeja Ch. opisana tutaj: http://www.kulinski.navsim.pl/art.php?id=2327&page=0 foto nr 2.(
Zamykając temat prostego kolektora. Muszę zwrócić uwagę na brak precyzji terminologicznej – zanim wytknie mi to któryś z Kolegów. W artykułach piszę o kolektorze chłodzonym wodą zaburtową – podczas gdy faktycznie jest to nie kolektor tylko tłumik wydechu pierwszego stopnia montowany z pominięciem kolektora.
Rozwiązanie to jest oczywiście znacznie doskonalsze od standardowych, tanich rozwiązań fabrycznych ponieważ:
a. Tworzy optymalne warunki opróżniania cylindrów (najmniejszy opór wypływu)
b. Istotnie zmniejsza hałaśliwość wydechu – w tej konstrukcji wydechu praktycznie nie słychać. Dominującym dźwiękiem jest hałas wtryskiwaczy, typowy dla układów zasilania z wtryskiem bezpośrednim
c. Tworzy ostatnią linie zabezpieczenia przed dostaniem się wody do cylindra.
Nasuwa się pytanie, dlaczego tego typu zintegrowane tłumiki nie są montowane w silnikach seryjnych. Odpowiedź brzmi: są czasami lub nie są, ze względu na duże koszty wykonania – nawet jeżeli użylibyśmy wytłoczek stalowych lub odlewów wysokociśnieniowych w kokilach.
Czasami wykonanie takiego kolektora jest niemożliwe – mamy świetny silnik, ale występuje kolizja z innym osprzętem na przykład filtrem oleju, pompą paliwową rozrusznikiem lub alternatorem. Wtedy postępujemy tak:
a. wykonujemy na wzór starego kolektora nowy z rur ze stali 316L
b. przygotowujemy miękką rurkę miedzianą fi=12 (od kilku do kilkunastu metrów) i w prowizorycznym przyrządzie z dwóch rolek przerabiamy ją na rurkę płaską
c. smarujemy stalowe rury pastą przewodzącą ciepło (lub owijamy specjalną taśmą – patrz tutaj: http://www.cyfronika.com.pl/kleje_pasty.htm) Następnie nawijamy na nie możliwie ściśle rurkę miedzianą. Każdy cylinder to osobna rurka. Rurki łączymy na trójniku lutując je lutem twardym
d. W ten sposób mamy faktyczny kolektor chłodzony cieczą – wylot z trójnika wprowadzamy do rury wydechowej za pomocą krótkiego odcinka wężyka gumowego.
e. Rozwiązanie jest bardzo pewne (testowałem je 3 sezony temu w silniku chłodzonym powietrzem) – ale wymaga bardzo duże precyzji i cierpliwości, aby nie załamać rurki miedzianej. Palnik na propan-butan może być nieoceniony.
Na koniec proszę o wybaczenie, że szkice nie zachowują wymiarów – robiłem je pod bujającym się pokładem "Zawiszy Czarnego" w Power Point’cie i trafienie myszką w linijkę było dużym wyzwaniem.
Powodzenia!
.T.L.
.T.L.
W artykule jest:
Węże firmy Vetus, które używałem mają oznaczenie SLANGx, gdzie x jest średnicą rury. Czyli SLANG50 to wąż fi=40 o średnicy wewnętrznej 40 mm – i taką rurę dobierzecie jako wyprowadzenie spalin z kolektora (http://viewer.zmags.com/publication/b84dd7ea#/b84dd7ea/84 strona 84)
Powinno być:
Węże firmy Vetus, które używałem mają oznaczenie SLANGx, gdzie x jest średnicą rury. Czyli SLANG40 to wąż fi=40 o średnicy wewnętrznej 40 mm – i taką rurę dobierzecie jako wyprowadzenie spalin z kolektora (http://viewer.zmags.com/publication/b84dd7ea#/b84dd7ea/84 strona 84)
Pozdrawiam. T.L.
Pytanie - komentarz. Panie Tadeuszu, dlaczego rura wydechowa jest spawana na stałe, a nie przykręcana – nie będzie jak czyścić tłumika.
Odpowiedź: po około 1000-1200 mth należyt zdemontować tłumik i do środka wsypać drobny żwir (ale nie piasek) + pudełko śrutu do wiatrówki. Lejemy wodę gorącą z detergentem. Zaślepiamy otwory płytką, której używaliśmy do kontroli jego szczelności. Wkładamy na tydzień w foliowej torbie do bagażnika samochodu i jeździmy. Kopiemy dół w ustronnym miejscu i wylewamy mnóstwo czarnego szlamu (sadza). Płuczemy tłumik – ścianki znów będą gładkie. Szpatułką od lodów czyścimy okna wydechowe. I na następne 1000-1200 mth.
W fabrycznych silnikach rury są przykręcane, ponieważ silnik może być zamawiany w wersji standard oraz high rise exhaust – patrz np. katalog firmy Beta Marine http://www.betamarinenc.com/index.php/engines/?next=3
W przypadku naszego jachtu od razu wiemy czego potrzebujemy – i oszczędzamy niepotrzebne wydatki na wykonanie i uszczelnianie odłączalnej rury.
Tadeusz
Napisał Pan, że w Vedze jest dwucylindrowy silnik, a na zdjęciu są trzy otwory wlotowe do tłumika. Czy to nie jest pomyłka?
Nie, to nie pomyłka. Kolega Marek Wąsik założył ten kolektor do siebie, ponieważ rozważa montaż w przyszłości 3 cylindrowej Kuboty, gdyby 482-ka okazała się za słaba. W Jego rozwiązaniu otwór jest zaślepiony stalową płytką. Alternatywnie tam zostanie zainstalowane odprowadzenie do przepływowego ogrzewacza wody do kuchni – rozwiązanie, które wcześniej przetestowaliśmy na "Donaldzie".
Pozdrawiam. T.L.